Porosity in Welding: Identifying Common Issues and Implementing Best Practices for Prevention
Porosity in welding is a pervasive issue that commonly goes undetected up until it triggers substantial issues with the honesty of welds. In this conversation, we will discover the crucial elements adding to porosity formation, examine its detrimental effects on weld efficiency, and discuss the ideal methods that can be taken on to minimize porosity event in welding processes.
Usual Reasons For Porosity

An additional frequent perpetrator behind porosity is the presence of pollutants externally of the base metal, such as oil, oil, or corrosion. When these pollutants are not efficiently gotten rid of before welding, they can vaporize and come to be entraped in the weld, triggering issues. Moreover, utilizing filthy or damp filler materials can present contaminations into the weld, adding to porosity issues. To mitigate these common sources of porosity, thorough cleaning of base metals, correct shielding gas selection, and adherence to ideal welding criteria are essential methods in accomplishing high-quality, porosity-free welds.
Impact of Porosity on Weld Quality

The visibility of porosity in welding can considerably jeopardize the structural integrity and mechanical properties of bonded joints. Porosity produces voids within the weld steel, damaging its general strength and load-bearing ability.
Among the main consequences of porosity is a decline in the weld's ductility and durability. Welds with high porosity levels often tend to display lower influence stamina and decreased capacity to warp plastically before fracturing. This can be specifically concerning in applications where the welded elements go through vibrant or cyclic loading conditions. Porosity can impede the weld's capacity to efficiently transfer pressures, leading to early weld failing and prospective safety and security dangers in critical frameworks. What is Porosity.
Ideal Practices for Porosity Prevention
To boost the architectural stability find here and quality of welded joints, what specific measures can be executed to decrease the event of porosity during the welding procedure? Making use of the right welding method for the certain material being welded, such as readjusting the welding angle and gun placement, can even more avoid porosity. Normal assessment of welds and instant remediation of any issues identified during the welding procedure are crucial techniques to avoid porosity and produce high-quality welds.
Relevance of Appropriate Welding Techniques
Implementing appropriate welding strategies is paramount in guaranteeing the structural integrity and quality of welded joints, building upon the structure of efficient porosity prevention actions. Too much heat can lead to boosted porosity due to the entrapment of gases in the weld pool. Furthermore, utilizing the ideal welding parameters, such as voltage, current, and take a trip rate, is essential for accomplishing sound welds with very little porosity.
In addition, the selection of welding process, whether it be MIG, TIG, or stick welding, ought to line up with the details needs of the project to make sure optimum outcomes. Proper cleaning and preparation of the base metal, in addition to choosing the ideal filler product, are view additionally crucial components of competent welding methods. By adhering to these finest methods, welders can reduce the danger of porosity formation and create top quality, structurally sound welds.
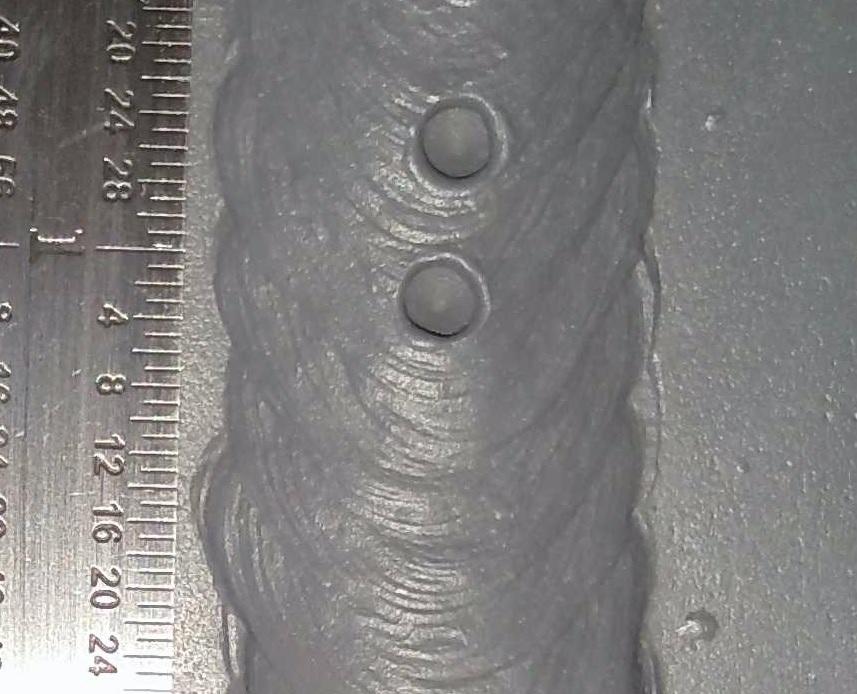
Evaluating and High Quality Control Actions
Quality assurance measures play an important duty in validating the honesty and integrity of welded joints. Testing procedures are necessary to find and protect against porosity in welding, making certain the strength and sturdiness of the final item. Non-destructive testing techniques such as ultrasonic testing, my sources radiographic testing, and aesthetic assessment are frequently utilized to determine prospective flaws like porosity. These methods enable for the evaluation of weld high quality without compromising the integrity of the joint. What is Porosity.
Carrying out pre-weld and post-weld evaluations is additionally important in preserving quality control criteria. Pre-weld evaluations entail confirming the materials, devices settings, and sanitation of the workspace to avoid contamination. Post-weld inspections, on the other hand, assess the last weld for any flaws, including porosity, and verify that it meets defined standards. Carrying out a comprehensive high quality control plan that includes thorough testing treatments and evaluations is extremely important to decreasing porosity issues and making sure the total quality of welded joints.
Verdict
To conclude, porosity in welding can be a common issue that affects the top quality of welds. By recognizing the common reasons for porosity and applying best methods for avoidance, such as appropriate welding strategies and screening actions, welders can make certain top quality and dependable welds. It is important to focus on avoidance approaches to decrease the event of porosity and keep the honesty of bonded structures.
Comments on “What is Porosity in Welding: Trick Aspects and Their Influence On Weld High Quality”